Speed sensor vibration velocity sensor , the vibration velocity is typically used to measure the vibration of the bearing , but there are a few cases in the shaft for measuring vibrations. How to install vibration velocity sensors do ? In the measurement of vibration velocity , if sensor is installed incorrectly or is not securely installed , themeasurement results will cause distortion due to vibration or damage caused by the speed sensor . So we
have to consider a good choice for vibration velocity sensor is installed. When the speed sensor is used to measure shaft vibration when installed in the field are usually taken with the hand , sticky water plasticine magnetic disk fixed , bolted in several ways . In the temporary vibration measurement , in most cases, hand sensors way , this method measured flexible , easy to use , especially when the number of the lack of vibration velocity sensors and sensor interchangeability bad, has a special advantage ; And this the disadvantage is that the test measurement error is relatively large, and the intensity of work is relatively large . Current speed sensor when measuring the vibration velocity , usually people will use Auto Temperature Sensor fixing screws directly on the bearing , not only can reliably measure the bearing at the top of the vibration in three directions , but also can be measured in two directions perpendicular to the plane of vibration this method is the best way to install the measure . Also has a different installation methods , due to the installation of the various conditions to determine that we have a good effect on manually installing a useful little plasticine paste Crankcase Position Sensor is also more convenient , you need to note that plasticine vibration velocity sensors can not be pasted into the vertical plane , and can only be fixed on a horizontal surface , as affected by temperature adhesive force , high temperature and the lower the adhesive strength will be significantly reduced, so it is not suitable for fixing the high temperature high pressure turbine rotor and reel measuring wheel speed Crankshaft Positioning Sensor bearing ; winter cold start , the bearing temperature is too low and it is not used . There is a similar permanent magnet sucker fixed speed sensor mounting , etc., when we observe the installation follow the rules is to measure the needs , the need to make sense of your environment changes , so that the vibration velocity sensor mounted only purpose is to more has the effect of reducing unnecessary errors.
The role of the crankshaft position sensor is to determine the position of the crankshaft, the crankshaft angle is. It is usually with the camshaft position sensor to work together - to determine the basic ignition timing
Engine Coolant Temperature Sensor
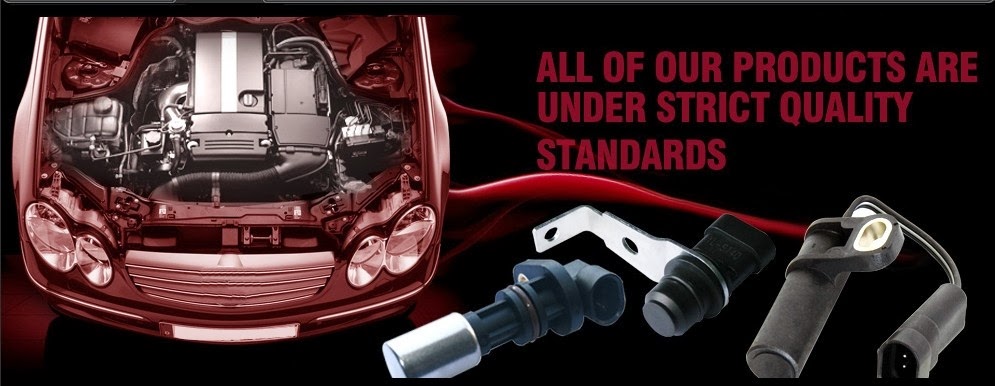
Engine Coolant Temperature Sensor
2013年10月27日星期日
What are static load cell features
The operating characteristics of the sensor by means of its static and dynamic characteristics reflected directly measuring system input is not constant over time and the system is present between the input and output static characteristics is the relationship . The static characteristics of the weighing sensor is divided into five parts. - Weighing Sensor Static One is repeatability, reproducibility refers to the so-called sensor input for full scale in the same direction repeatedly changed, the resulting curve degree of inconsistency . In those who are weighing sensor sensitivity and linearity, sensitivity sensor static characteristics is an important indicator . Which is defined as the amount of output incrementincrement causes the ratio of the corresponding input increment . S is a sensitivity. The linearity of the sensor is output and input of the actual relationship between the degree of the curve -fit straight line deviation . Defined as the whole range of the actual characteristic curve and the maximum deviation between the fitted line with the full-scale value of theratio of the output value . Static characteristics of the load cell is important to drift, the same amount of the input , Crankshaft Sensor output varies with time , this phenomenon is called drift, and other similar weighing sensor drift mainly generated by Car Temperature Sensor is the sensor their structural parameters and application ambient temperature , humidity and other effects .Weighing sensor input changes from small to large and from large to small input and output characteristic curve during the input phenomenon does not overlap a static characteristic is the sensor end , the input signal for the same size , Motor Position Sensor output signal of the positive and negative stroke not of equal size , this difference is called hysteresis difference . - Static characteristics of the load cell refers to the static input signal , the output of the load cell and the input of a relationship between . Because when both input and output , and time-independent , so that the relationship between them , the static characteristics of the load cell can be a free time variable algebraic equations , or-axisinput,theoutputofitscorresponding volume plotted as the ordinate andcharacteristic curvesdescribed.Characterization of the sensor static characteristics of the main parametersare:repeatability, sensitivity, linearity. Then the impact of the load cell measuring effects and selection of the key elements of that is that a few key points
How long can the displacement sensor life
We live in an age of advanced science and technology , should be carried out in various fields necessary for detection and analysis . Displacement sensor applications are increasingly widespread . That how to make it last longer displacement sensor ? Both methods are based on the piezoelectric power generator , a micro- electromechanical systems (MEMS) cantilever converted into electrical energy to mechanical motion , and the motion of the cantilever can be driven in different ways . One is with a radioisotope , and another vibrationcollected with the environment . All self-powered communication nodes must maintain their memory state , periodically send its status . This requires 0.1 microwatts to 1 milliwatt of power. Cornell University researchers with a small amount of nickel -63 (Ni-63) to join its radioisotope neutrons in the nucleus made of a piezoelectric generator. It can be a beta particle radiation harmless to maintain every 3 minutes 5mW RF pulses . Up to 100 years of its life . Netherlands an Imac nanoelectronics research center created a wireless , autonomous temperaturesensor. Nitrogen compound aluminum vibration collector. Displacement vibration energy collected by Shaft Position Sensor generally require a specific vibration frequency of 1 micron . The sensor can measure
the temperature every 15 seconds , and the data to the base station of more than 15 m . However, the sensor can not be packaged under atmospheric pressure , vacuum packaging in order to be up to 85 micro watts. Both programs are considered to be the original innovation, especially in the industrial sector after promising a program that is promising . This reminds me of the importance of interdisciplinary . In China, it was also studied low -power sensors,self-powered sensors, Crank Position Sensors nodes. However, people were asked to engage in computer power plus local power control , engage people to lower the voltage electronics , modify the circuit , who were asked to engage in strategic research needs of people who engage inmaterial made of certain materials CMOS process modifications . All of these ideas are good , that is, as stated above do not form a Camshaft Position Sensorsolutions and experimentally demonstrate its feasibility. Our old gave me a feeling of floating on top , or nowhere near enough analogy something more , something to talk about on paper more. Recently, I reviewed adomestic article about software fault tolerance. His talk about the real software fault-tolerant technology, but between the methods to study various software fault-tolerant scheduling algorithm . You did not study a software fault-tolerant way , how do you choose , scheduling it ? On paper can only be empty talk
the temperature every 15 seconds , and the data to the base station of more than 15 m . However, the sensor can not be packaged under atmospheric pressure , vacuum packaging in order to be up to 85 micro watts. Both programs are considered to be the original innovation, especially in the industrial sector after promising a program that is promising . This reminds me of the importance of interdisciplinary . In China, it was also studied low -power sensors,self-powered sensors, Crank Position Sensors nodes. However, people were asked to engage in computer power plus local power control , engage people to lower the voltage electronics , modify the circuit , who were asked to engage in strategic research needs of people who engage inmaterial made of certain materials CMOS process modifications . All of these ideas are good , that is, as stated above do not form a Camshaft Position Sensorsolutions and experimentally demonstrate its feasibility. Our old gave me a feeling of floating on top , or nowhere near enough analogy something more , something to talk about on paper more. Recently, I reviewed adomestic article about software fault tolerance. His talk about the real software fault-tolerant technology, but between the methods to study various software fault-tolerant scheduling algorithm . You did not study a software fault-tolerant way , how do you choose , scheduling it ? On paper can only be empty talk
For you to resolve the five sensor software technology
Digital sensor has a strong anti-interference ability , signal transmission distance , goodstability of these advantages, because it is being used to digital information technology into the sensor , and Cooling Temp Sensor software technology levels are therefore plays an important role inside . Under normal circumstances we have five kinds of software technology , give you a brief introduction below : scale conversion technologies: analog signal by the analog-digital conversion obtained after a series of digital , it must be converted with dimensionless data to calculate , display, which need to use scale conversion technologies. Digital zeroing technique : using a variety of procedures to achieve zero drift , gain, offsetcalibration drift . Digital filtering techniques : Car Temperature Sensor analog output signal, the analog-digital conversion into the microprocessor , the normally sharp pulse entering into therandom noise and the like , must be weakened and filter , the digital filter technology to solve this shortcoming . Temperature compensation : Expression temperature established mathematical model , with the difference between the other mathematical processing method , temperature compensation can be effectively achieved , depending on the effect of temperature on Auto Temperature Sensor output size. Nonlinear compensation technique : the measured characteristic curve, piecewise interpolation , if the interpolation points is reasonable and sufficient , excellent linearity can be obtained . Integrated use of these five sensor software technology , for the design of the sensor is also helpful, software is the core, the hardware is the foundation, both have to take into account
Sensor type and application conditions , you should follow the recommended calibration method
The method of calibration . Taking into account all the factors , such as sensor type and application conditions , you should follow the recommended calibration method : According to the operator's judgment , gas sensors surrounding gas is fresh , there is no abnormalcondition exists , then, the instrument indication near zero ( reading ) , zero setting process can be skipped. When in doubt , use a plastic bag aroundCamshaft Position Sensor to get some considered to be " fresh " air. This is a very quick and easy process . This method for the difference between true and false alarm warning is very effective . There is an advantage that the compressed air , the gas in the bottle is easy to control and easy to carry . The device is easy and convenient to get air . Such a small amount of air in the meaning of hydrogen and nitrogen , carbon monoxide , carbon dioxide and some other interfering gases . However , this gas is characterized by low humidity , the solution used in the sampling system with activated carbon filters are used to filter out unwanted wet gas in the gas and water vapor. After this process , we can use the gas for various types Car Temperature Sensor calibration . However, it should be noted that carbon monoxide gas and not through a filter with activated carbon and filtered . Therefore, the rule states: cylinders of carbon monoxide gas with the surrounding environment must be the same content . In addition , the use of soda ash filter can filter out carbon monoxide. Since the sampling system using the soda ash line filter can filter out although an oxygen gas is usually very pure man , but it can not be used for solid-state Engine Water Temperature Sensor and
photoionization detectors, because such sensors require the gas contained in the sampling some water vapor. A simple way to solve this problem is to use the sampling system pipeline damp tissue paper . Its role is to make the wet stream sample , the sensor has sufficient water vapor. Another option of using NAFION tube
photoionization detectors, because such sensors require the gas contained in the sampling some water vapor. A simple way to solve this problem is to use the sampling system pipeline damp tissue paper . Its role is to make the wet stream sample , the sensor has sufficient water vapor. Another option of using NAFION tube
2013年10月24日星期四
Explosion-proof sensor works is what Source: Sai Siwei Posted at 2013-6-25 Sensor Networks
For the use of sensors in explosive situations , in order to avoid an explosion, usually chosen with explosion-proof requirements. Explosion-proof sensor has the following three main methods , namely, control explosive gases, control limits and control detonated explosive source following these three methods work done under a brief introduction : 1, control explosive gas works in a sealed explosion-proof cabinets , full of clean gas without explosive gas or inert gas , and keep the box outside the box pressure slightly above atmospheric pressure , the sensor is installed in the box . Type represents a positive pressure -proof method Exp. 2, the control principle is based on the explosion limits Exd GB , Crank Position Sensor housing is designed to flameproof standard housing , instrument design standards by flameproof housing , according to standard sternly design, manufacture and assembly of all management approach to the implementation process , within the housing so that the explosive attack risk Buzhi Yu stimulate housing outer gas explosion. Explosion -proof approach to the design and manufacturing standards extremely harsh, and assembly, wiring and maintenance procedures are very strict. The approach determines the flameproof electrical equipment , instrumentation often very strict operation should power outages , etc., but many cases are also the most useful approach. 3, the control detonation source works by applying barrier to isolate wiring from Engine Temperature Sensors is processed in electricity distribution , will be supplied to the electric field sensors energy can neither be restricted enough to detonate a spark occurs , the instrument can happen enough to detonate exterior temperature rise within safe limits . In accordance with international norms and norms of the country , when the safe side of the gate area of the connected equipment safely attack any obstacle , the real safe way to ensure that the risk -site explosion -proof safe. Need to remind you to consider in choosing the sensor due to the use of different occasions and configuration , on-demand options intrinsically safe , explosion-proof Crankshaft Positioning Sensor and instrumentation , but also to the supplier needs to Ex- certification.
Dynamic torque sensor installation
Dynamic torque sensor installation:1, the use of the environment: Car Sensors should be installed in an ambient temperature of 0 ℃ ~ 60 ℃, relative humidity less than 90%, non-flammable and explosive chemicals environment. Should not be installed in the strong electromagnetic interference in the environment. 2, Installation: (1) Horizontal mounting: (2) vertical mounting: 3, Connection: Engine Water Temperature Sensor with power equipment, the connection between the load equipment (1) flexible pin coupling connection, this connection structure simple, easy processing, easy maintenance. Trace caused to compensate for shaft misalignment relative offset, and can play a minor role in damping. For medium load, high-speed operation starting Car Temperature Sensor, the working temperature -20-70 ℃. (2) rigid coupling connection which forms a simple structure, low cost, no compensation performance, not buffer damping of high mounting accuracy of the two axes. For vibration small working conditions.
Introduction and use of pressure sensors Precautions
In daily life use and purchase pressure sensors require all it has a certain understanding, particularly when in use, if there is no understanding of good note, it is easy to cause the machine to malfunction or damage to the sensor from occurring, or is causing measurement accuracy decreased or even data is wrong. Pressure sensors, that is, when sensing the pressure, the pressure can be utilized to convert the sensor output signal, which is based on this principle manufactured piezoelectric effect, generally, piezoelectric sensors can measure only dynamic pressure can not be applied in a static measurement occasions, this is because when subjected to mechanical force generated when the role of the charge only in the loop when it has infinite input resistance, this time can be preserved. In everyday industrial practice, Engine Temp Sensor has become a very widely used sensors, many industries in order to control quality of the environment inside, have invested heavily use it. Polarization effect of the pressure sensor is based on developed. Well, this polarization effect is how it goes? Crystal, I believe we are all familiar with it. Crystals are anisotropic, not a crystal it is isotropic. When a crystal of some media in a certain direction by the action of mechanical force causing it to change the shape of, this will form a polarization effect . When the mechanical external force disappears, the crystal will return to the original uncharged state. The so-called polarization effect refers to the time when subjected to mechanical force, a number will appear inside the crystal or live effectMany industries in the use of Camshaft Positioning Sensor unit when there will be a big problem, so you understand it well before using in the course of matters that need attention. First, to avoid corrosion and temperature transmitter with having contact with the medium in order to avoid excessive damage to it; pressure guide tube mounting position preferably in the temperature fluctuations smaller occasions; in the measurement of some of the media has a high temperature, it must be connected to the condenser, it is because you want to avoid the transmitter to work when the temperature exceeds a certain limit; want to keep the catheter in the unobstructed; when used in the cold winter, if the transmitter is installed outdoors, then have a good antifreeze measures be taken, which is to prevent impulse mouth for the sake of the liquid causes freezing because its volume swell up, so easy to damage the sensor; when the user terminal, the cable should wear over waterproof connector or is it about sex tube and then sealed to tighten the nut, it is possible to prevent liquid from leaking into these things through the cables inside the housing of the transmitter. Now speaking about the measurement of liquid pressure and gas pressure precautions, we have to distinguish clearly. Measuring fluid pressure, when the pressure taps must be open in the flow line where the side surface, which is to prevent dross precipitated sake, there is installed at this time where the transmitter should prevent other liquids, shock, because Cooling Temperature Sensor excessive damage. In the measurement of gas pressure when the pressure port must be open in the top position of the pipeline process, note that this is the time with the measuring fluid pressure difference, then the transmitter must be installed in the upper part of the process piping, which is convenient have accumulated liquid may be easily injected into the flow line to go .....
The advantage of digital load cell
First, the transmission distance, communication speed, the effect is significant anti-cheating traditional analog load cell output signal is small , typically millivolts during transmission due to cable resistance effects , there is loss of signal , but also susceptible to ambient interference , it is not for long-distance transmission. Its signal cheating a lot, usually difficult to control. The digital load cell signal output is digital, not only a high level , the impact of interference is very small, and it is the use of field bus technology, communication speed is super fast , but also with a communication error correction function, due to the confidentiality of communications protocols , cheating is basically impossible , so get a high data reliability . Second, anti-interference ability , high reliability, good lightning performance analog sensor output from the instrument power supply , power quality affected by the instrument . Between them susceptible to electromagnetic interference and surges. Instability of the power supply of Shaft Position Sensor output is also great, likely to cause instability in the output , the high voltage transient will cause the sensor damage. Digital sensor with a new welding manufacturing technology, which is also filled with helium safety protection circuit , a very high degree of protection . In order to prevent lightning surge interference , which uses the output voltage of the instrument reprocessing meet the sensor supply voltage requirements , so that the output signal becomes stable , the sensor will not be damaged . Three , eliminating calibrated load cell to get the scene, there is no suitable counterweight system calibration is generally difficult , if not then its calibration , the error will be great. Engine Coolant Temp Sensor during the live connection has loss, so must be carried out on-site calibration . And now digital sensors can dispense the job , because it has been used in the production of standard dynamometer was calibrated , and its output is the corresponding standard values . Since it does not substantially project in the transmission loss, so the read value is the actual measurement value , so it can save the calibration of the link. Fourth, you can work uninterrupted digital sensor error function it has a fault , once fails, it will output the signal to the instrument , the instrument signal is received , you can abandon its value , to automatically start uninterrupted work, can still guarantee a certain accuracy , the user can always know which sensor needs to be replaced , will not cause the production stagnant . Coolant Temperature Sensor can not meet that requirement , once the fault will cause production downtime , affecting plant efficiency. Five , easy maintenance, low overall cost of using digital load cell with a standard cable plug, both to ensure the protection level, and the replacement of the sensor or the cable is very convenient, but because of its digital output , without the impact of cable length . The analog temperature compensation of the sensor it is together with the cable , the cable will be connected after damage caused by errors , so many sensors are connected together with cable , replacement when it need to re- stringing , very inconvenient to use . It now appears that , although the digital sensor more than analog sensor circuit board , but not in the course of calibration , commissioning time will be greatly reduced , higher reliability , but also has a self- diagnostic function, can not be shut down for some production units , it also ensures uninterrupted work , saving production costs, so in general, it uses the overall cost is lower than the analog sensors .
How to select the flow sensor
Liquid density sensor means can feel liquid density , and it can be converted into an output signal that can be used sensors, liquid density sensor can be divided into six categories: capacitive, ultrasonic , tuning fork , resonant , radiation type and vibrating tube liquid Shaft Position Sensor . Capacitive liquid density sensors it is not based on the same liquid sample , the standard different buoyancy body , this will lead to an object connected with standard two capacitance change in the distance between the plates , and resultant capacitance changed. Because different liquid density sensor for different occasions , so in practical application , it should be depending on the nature of the liquid to be measured also on the measurement accuracy requirements, and so the situation and the choice of suitable sensors. Ultrasonic Density sensors it is higher than the frequency of the ultrasonic mechanical waves of 20kHz and an ultrasonic wave only may be in the form of propagation in a liquid medium . It is for the phase , frequency, speed and attenuation properties of the medium will be subject to impact , so, it can be based on the ultrasonic propagation properties and some of the correspondence between the density of the liquid to measure the density of the liquid . Its main advantages are: it can achieve non-contact measurement, the measurement accuracy is relatively high, relatively fast response ; and it has no moving parts , so the stability of the measurement is better ; it is not radioactive , there is no harm to the human body . The disadvantage is that there are impurities in the liquid medium , for example , bubble can lead to severe attenuation of the ultrasonic signal ; precision measurements in viscous media , the need to consider the impact of medium viscosity ; it will make some measurements lead to instability .Auto Temperature Sensor it is based on the liquid density in the liquid , the mass of small tuning fork vibrates, its inherent frequency change , so to measure the density of the liquid . To obtain high accuracy measurement results , it is necessary to detect the resonant frequency when the change is small , it is necessary to design rational vibrating unit , so that the vibration unit can be a relatively high mechanical quality factor . Fork usually made of glass or stainless steel . Resonant resonant liquid density sensor measuring principle is based on the vibration characteristics of a harmonic oscillator to work . In operation, the resonator can be equivalently used as a single degree of freedom system , with the natural frequency of the vibration , the natural frequency of the system with the system is only the equivalent elastic modulus and the equivalent mass . Resonant liquid density sensor measuring principle is the liquid through the system and the elastic contact with sensitive components cause changes in the system of equivalent mass , resulting in changes in the natural frequency of the system . Measuring system according to a fixed frequency variation can know the density of the liquid to be measured . Liquid Density Sensor ray rays Liquid Density Sensor The main disadvantages are: it is not very high resolution ; it needs a relatively long time have stability ; It requires radioactive ray source . Its advantages are: the liquid flow sensor does not generate resistance to the flow size is not limited, and it can measure the density of the multiphase fluid ; when it is not in contact with the measurement of the liquid under test , it can be realized non-contact measurement . Liquid Cooling Temperature Sensor vibrating tube vibrating tube type liquid density sensor can reasonably be arranged drive member , to allow the inside tube vibration in the same plane , it is the measured density of the liquid flowing in the tube the average mass density . The sensitive element is that it uses a long tube vibration , its length is about 20 times the diameter .
2013年10月23日星期三
How to install vibration velocity sensors
Speed sensor vibration velocity sensor , the vibration velocity is typically used to measure the vibration of the bearing , but there are a few cases in the shaft for measuring vibrations. How to install vibration velocity sensors do ? In the measurement of vibration velocity , if sensor is installed incorrectly or is not securely installed , the measurement results will cause distortion due to vibration or damage caused by the speed sensor . So we have to consider a good choice for vibration velocity sensor is installed. When the speed sensor is used to measure shaft vibration when installed in the field are usually taken with the hand , sticky water plasticine magnetic disk fixed , bolted in several ways . In the temporary vibration measurement , in most cases, hand sensors way , this method measured flexible , easy to use , especially when the number of the lack of vibration velocity sensors Engine Temperature Sensor interchangeability bad, has a special advantage ; And this the disadvantage is that the test measurement error is relatively large, and the intensity of work is relatively large . Current speed sensor when measuring the vibration velocity , usually people will use Engine Temp Sensor fixing screws directly on the bearing , not only can reliably measure the bearing at the top of the vibration in three directions , but also can be measured in two directions perpendicular to the plane of vibration this method is the best way to install the measure . Also has a different installation methods , due to the installation of the various conditions to determine that we have a good effect on manually installing a useful little plasticine paste the speed sensor is also more convenient , you need to note that plasticine vibration velocity sensors can not be pasted into the vertical plane , and can only be fixed on a horizontal surface , as affected by temperature adhesive force , high temperature and the lower the adhesive strength will be significantly reduced, so it is not suitable for fixing the high temperature high pressure turbine rotor and reel measuring wheel Car Temperature Sensor bearing ; winter cold start , the bearing temperature is too low and it is not used . There is a similar permanent magnet sucker fixed speed sensor mounting , etc., when we observe the installation follow the rules is to measure the needs , the need to make sense of your environment changes , so that the vibration velocity sensor mounted only purpose is to more has the effect of reducing unnecessary errors
What are the application Humidity Sensor
Humidity sensor is able to feel the water vapor content in the gas and used to convert the output signal of the sensor. With the realization of modernization , it is difficult to find a field unrelated to the humidity , the humidity sensor for measuring or controlling the relative humidity of the gas or absolute humidity, dew point and so on. Can indirectly control the temperature . Below its typical application for an introduction. ( A ) in the humidity measurement system application ( a ) below 70 ℃ ( normally at -40 ℃ above ) , if relatively clean environment , the use of polymer sensors, polluting the use of ceramic sensor ( heating washing of regeneration type ) . Heating the cleaning process as it exists , can not be continuously measured , and the large energy consumption (1 ~ 10W). However, long life, use the optional heated sensor clean cycle is longer , such as chlorine oxy apatite Camshaft Positioning Sensor , 2 ~ 3 months wash , in addition, internal heat than the outer heat and low energy consumption . ( 2 ) In the range of 70 ~ 100 ℃ measured humidity , washing with a heating ceramic sensor , to improve the accuracy of linear and temperature compensation. In order to achieve more accuracy will have with the microcomputer. In hot and humid heat required frequent cleaning, such as more than 80% RH , the need to 30S cleansing once daily, preferably equipped with automatic cleaning device heating . ( 3 ) in the range of 100 ~ 150 ℃ humidity measured in the international community , mostly made of ceramic Camshaft Position Sensortemperature and humidity instrument . ( Two ) in the industrial automatic control application process in order to improve product quality and energy , usually in the product drying system , humidity control reactors , boilers, water vapor leak detection, integrated circuits or the head of the air-conditioning plant mostly using ceramic Crankshaft Sensor Replacement control ; variety of air conditioning systems, medical systems and humidity control can be polymeric or ceramic humidity sensor . ( Three ) in a steam leak detection systems used in thermal power stations , nuclear power plants, steam locomotives , boilers and other high temperature and pressure equipment , in order to prevent leakage, prevent accidents , humidity sensor can be used for leak detection . ( Four ) in the other systems used in home appliances dew condensation detection sensor can be used as tape recorders , car windows, condensation , frost detection. Humidity sensor applications driving the need for microelectronic circuit package failure mechanism analysis , due to IC failure and humidity have a great relationship .
How to correctly judge the photoelectric sensor output no signal
Photoelectric sensor is a photoelectric sensor element as a sensing element , widely used in the automation field . Photoelectric sensors for material handling, error detection , process manufacturing automation, object detection can also be used over long distances or fault is detected. Photoelectric sensors detect the distance of the object has a unique advantage , but in the specific use of the environment, there will be some technical problems , which we need methodical technical judgment. In the application of photoelectric sensors to detect objects in the distance , a lot of users will encounter problems when using photoelectric sensors to detect objects is no output signal after , making it impossible for subsequent data analysis. Most people see no signal sensor output may often be some wrong judgment , such as some people on the direct determination of the sensor bad reason. But the reason is not all like that, photoelectric sensor detects an object after no output , there may be many reasons , we need to do it step by step investigation . The first thing to consider is wiring or configuration problems . For beam photoelectric sensor must be cast by the light unit and a light unit used in combination with both ends requires power ; while retroreflective type sensor probe and must be retroreflective sheeting used in combination ; same time, the user must provide a stable power supply to the sensor , if it is DC power supply , you must confirm the positive and negative , should the positive and negative connection error will cause the output signal is not . The reason analysis is to consider photoelectric sensor itself , we also need to consider the problem is to detect the location of objects , if the detected object is not in the detection area , so that the detection is futile. Test object must be detected in the sensor area , that is, can sense the optical range. Secondly, we must consider the optical axis of Crankcase Position Sensor there is no alignment problem , on the radio type of light-emitting portion and a light receiving unit must be aligned with the optical axis , the corresponding portion of the retroreflective Camshaft Position Sensor must be aligned with the optical axis and the reflector . The same should also consider whether the detected object is the standard sensing object or minimum standard sensing object , object detection can not detect an object less than the minimum standard , thus avoiding lead shot , reflective not well detect transparent objects , like a reflection on detecting the color of objects is required, the deeper the color , the more recent detection distance . If the above conditions can be excluded to make it clear , we need to do is to detect environmental disturbances . Such as light intensity can not exceed the rated range ; if there is dust environment of the scene , we need our regular cleaning optical sensor probe surface ; or Crankshaft Position Sensor close fitting , mutual interference ; there is a relatively large impact that electrical interference , if surrounded power equipment , interference must have the appropriate anti-jamming measures . If you have done the above one by one investigation , these factors can be explicitly excluded or no signal output , it is recommended to return factory testing to determine .
On the humidity sensor applications
Currently on the market humidity sensor applications is also increasing. Humidity sensors are used to measure or control the relative humidity of the gas or absolute humidity, dew point and so on. Can indirectly control the temperature . ( A ) in the humidity measurement system application ( a ) below 70 ℃ ( normally at -40 ℃ above ) , if relatively clean environment , the use of polymer sensors, polluting the use of Camshaft Position Sensor ( heating washing of regeneration type ) . Heating the cleaning process as it exists , can not be continuously measured , and the large energy consumption (1 ~ 10W). However, long life, use the optional heated sensor clean cycle is longer , such as chlorine oxy apatite ceramic sensor , 2 ~ 3 months wash , in addition, internal heat than the outer heat and low energy consumption . ( 2 ) In the range of 70 ~ 100 ℃ measured humidity , washing with a heating Engine Coolant Temp Sensor , to improve the accuracy of linear and temperature compensation. In order to achieve more accuracy will have with the microcomputer. In hot and humid heat required frequent cleaning, such as more than 80% RH , the need to 30S cleansing once daily, preferably equipped with automatic cleaning device heating . ( 3 ) in the range of 100 ~ 150 ℃ humidity measured in the international community , mostly made of ceramic Automotive Temperature Sensors temperature and humidity instrument . ( Two ) in the industrial automatic control application process in order to improve product quality and energy , usually in the product drying system , humidity control reactors , boilers, water vapor leak detection, integrated circuits or the head of the air-conditioning plant mostly using ceramic humidity sensor control ; variety of air conditioning systems, medical systems and humidity control can be polymeric or ceramic humidity sensor . ( Three ) in a steam leak detection systems used in thermal power stations , nuclear power plants, steam locomotives , boilers and other high temperature and pressure equipment , in order to prevent leakage, prevent accidents , humidity sensor can be used for leak detection . ( Four ) in the other systems used in home appliances dew condensation detection sensor can be used as tape recorders , car windows, condensation , frost detection.
Automobile engine temperature sensor
Car engine is a one of the most important car , its temperature for a car 's fuel consumption also has a decisive influence . Not to say that high temperatures will fuel more, in fact, the temperature is too low will lead to an increase in fuel consumption . Car engine work required to have normal temperatures ( 80 to 90 ) , Camshaft Positioning Sensor on the engine is particularly important. If the temperature is too high , the engine cooling system can automatically change the cooling water , increase the heat , remove excess heat ; Conversely, reducing the circulation of cooling water to maintain the necessary temperature . To achieve the main components of the cycle automatically change the engine Crankshaft Sensor Replacement, thermostat valve thermostat and magnetic fan. Cold start , the magnetic fan is stopped , the thermostat valve is in the down state , the engine coolant in the engine water jacket only in small cycles , easy to heat , while computers were affected Camshaft Position Sensor temperature index , will be issued to increase fuel injection, increasing the idle valve opening instruction , increase the engine speed is conducive to allow the engine to heat up quickly ; temperature is normal , the fuel injection quantity and idle valve opening are restored to normal. When the temperature exceeds 80 to 90 degrees ( of the vehicle slightly different) , the thermostat valve is opened , the engine water jacket through which coolant flows through the radiator thermostat valves bigger radiator circulation of air generated by the vehicle flow , away a lot of heat , to maintain normal temperature of the coolant . Slow or even stop , but if the speed does not stall , no flow of air to help dissipate heat , the engine will quickly heat up, then issued a directive to the magnetic temperature sensor helps radiator cooling fan starts .
Capacitive oil sensor line
Currently online oil pollution sensor is still in trial stage theory , the use of capacitive measurement method, ie detection software support, integrated by measuring the change in dielectric constant of oil to determine the extent of contaminated oil . Its working principle is: the oil as a dielectric , as new oil, and the oil 's dielectric constant is different when the oil change will cause a change in Crankcase Position Sensor via C / V conversion put this slight change frequency demodulation of the DC signal, the data acquisition circuit samples pre- amplification , A / D converter , sent to the microcontroller after the class consisting of hardware and software data processing system . System based on test data, analysis calculated determination of various types of oil pollution in the upper and lower threshold level target value by including algorithms for intelligent analysis and processing procedures , by the LCD Monitor Report User quantitative ( pollution index value ) and qualitative ( well, available , scrapped ) test results. Because the causes of oil pollution and environmental factors more complex , so the principle of Engine Water Temperature Sensor in the production practice has not been very good application. For example : As the engine piston blow-by , the delay of fuel injection causes the exhaust gas treatment system of exhaust gas into the cylinder , or a leak in the high pressure common rail diesel standard 2 contaminated oil, will cause the viscosity of the oil drop , but the oil dielectric no effect on dielectric constant and density .
Describes the characteristics of the thermocouple temperature sensor
Temperature sensor using the current very high rate in the industrial production , industrial development and use Crankshaft Positioning Sensor is currently running efficiency is very convenient to use the industrial automation , the temperature sensor is currently preferred product the thermocouple , the thermocouple is a a sensor measuring temperature , and thermal resistance are the same as the Camshaft Positioning Sensor , the two different materials a and B conductors or semiconductors welded together to form a closed loop, when two conductors a and B attachment between points 1 and 2 when the temperature difference between the two will generate an electromotive force , and thus forming a loop of current, a phenomenon known thermoelectric effect . Is called the Seebeck effect . Thermocouple probe is to use this effect to work . First, the nature of the signal , the thermal resistance is the resistance itself , temperature changes, the thermal resistor to generate positive or negative change in resistance ; the thermocouple, the induced voltage changes, he is changed with temperature . Second, Engine Water Temperature Sensor detect the temperature range is not the same, the general resistance test temperature range 0-150 ° , the maximum measuring range of up to 600 degrees ( of course, negative temperature can be detected ) . Third, from the material of resistance, which is a metal material having a metallic material changes in temperature-sensitive , bimetallic thermocouple materials , both of two different metals , due to temperature changes in the two wires of two different end generates a potential difference . Four , PLC corresponding thermal resistance and thermocouple input module is not the same , this sentence is not a problem , but generally have direct access to the PLC 4 ~ 20ma signals, and thermal resistance and thermocouple generally with transmitter only access PLC. If you do not have access to the DCS , then use the transmitter up ! Thermal resistance is the RTD signal , thermocouple is TC signal ! Five , PLC also has RTD and Thermocouple modules can be directly input resistance and thermocouple signals. Six , thermocouple J, T, N, K, S and other models , there are specific resistance expensive , there are also cheaper than the resistance , but the count compensation wire , thermocouple total cost will be high .
Barometric altitude sensor Features
Barometric altitude sensor is a change in the use of pressure sensors to measure the height of a. When measuring the height advantage of the processor because of the need to get through a formula to calculate the height values, so in the general election when Shaft Position Sensor output digital signals are used to. HM products mainly used in floor outdoor climbing altimeter GPS positioning tables, outdoor climbing phones, hunting cameras, parachutes, meteorological equipment and other fields. Main features: barometric Auto Temperature Sensor is achieved by changes in air pressure Camshaft Position Sensor to measure the height, so the measurement process from the impact of obstacles, measure the height range, easy to move, can be an absolute altitude measurements and relative height measurements. By pressure and temperature to calculate the height errors are relatively large, especially in the near-surface measurement, by the wind, humidity, dust particles and other effects, a high degree of accuracy of measurement. Very much affected, at high altitude measurement accuracy has improved.
Temperature sensor in the engine room applications
Temperature sensor in the engine room applications, primarily for monitoring a program on the host reaches a certain value after the alarm application program has a great advantage, and spread to a number of areas .
Room temperature and humidity as computer equipment normal operation of the necessary conditions , we must in the engine room of a reasonable location to install temperature and humidity Cooling Temperature Sensor , in order to achieve the temperature and humidity for 24 hours real-time monitoring , and can be in the control room to monitor the host real-time display of each location of temperature and humidity measurements. Once a value in excess of the preset upper and lower limits of temperature and humidity in the monitoring host location by changing the value of the corresponding color alarm . In the overall monitoring of the entire Crankcase Position Sensor and humidity conditions in the new fan inlet and the main air conditioner return air, humidity and temperature transmitters were installed to detect the temperature and humidity. Except for the room temperature and humidity monitoring surveillance , but also can be widely used as bio-pharmaceuticals , sterile room, clean room , telecom banks, libraries , archives, Museum, intelligent buildings and other industries need a place to monitor temperature and humidity and fields. Application advantages open communications protocol, system expansion . Configuration software interface, system stability is guaranteed. Software feature-rich, practical, convenient maintenance and feature upgrades . Using high temperature and humidity transmitter, high accuracy and stability . Digital signal transmission, wiring convenience , the signal transmission distance .
Room temperature and humidity as computer equipment normal operation of the necessary conditions , we must in the engine room of a reasonable location to install temperature and humidity Cooling Temperature Sensor , in order to achieve the temperature and humidity for 24 hours real-time monitoring , and can be in the control room to monitor the host real-time display of each location of temperature and humidity measurements. Once a value in excess of the preset upper and lower limits of temperature and humidity in the monitoring host location by changing the value of the corresponding color alarm . In the overall monitoring of the entire Crankcase Position Sensor and humidity conditions in the new fan inlet and the main air conditioner return air, humidity and temperature transmitters were installed to detect the temperature and humidity. Except for the room temperature and humidity monitoring surveillance , but also can be widely used as bio-pharmaceuticals , sterile room, clean room , telecom banks, libraries , archives, Museum, intelligent buildings and other industries need a place to monitor temperature and humidity and fields. Application advantages open communications protocol, system expansion . Configuration software interface, system stability is guaranteed. Software feature-rich, practical, convenient maintenance and feature upgrades . Using high temperature and humidity transmitter, high accuracy and stability . Digital signal transmission, wiring convenience , the signal transmission distance .
Automobile engine temperature sensor
Car engine is a one of the most important car , its temperature for a car 's fuel consumption also has a decisive influence . Not to say that high temperatures will fuel more, in fact, the temperature is too low will lead to an increase in fuel consumption . Car engine work required to have normal temperatures ( 80 to 90 ) , Coolant Temp Sensor on the engine is particularly important. If the temperature is too high , the engine cooling system can automatically change the cooling water , increase the heat , remove excess heat ; Conversely, reducing the circulation of cooling water to maintain the necessary temperature . To achieve the main components of the cycle automatically change the engine temperature Coolant Temperature Sensor, thermostat valve thermostat and magnetic fan. Cold start , the magnetic fan is stopped , the thermostat valve is in the down state , the engine coolant in the engine water jacket only in small cycles , easy to heat , while computers were affected Crankshaft Sensors temperature index , will be issued to increase fuel injection, increasing the idle valve opening instruction , increase the engine speed is conducive to allow the engine to heat up quickly ; temperature is normal , the fuel injection quantity and idle valve opening are restored to normal. When the temperature exceeds 80 to 90 degrees ( of the vehicle slightly different) , the thermostat valve is opened , the engine water jacket through which coolant flows through the radiator thermostat valves bigger radiator circulation of air generated by the vehicle flow , away a lot of heat , to maintain normal temperature of the coolant . Slow or even stop , but if the speed does not stall , no flow of air to help dissipate heat , the engine will quickly heat up, then issued a directive to the magnetic temperature sensor helps radiator cooling fan starts .
How to choose the correct humidity sensor
Human survival and social activities and humidity are closely related, it is important to measure the humidity , the humidity sensor and thus also the birth , it can feel the water vapor content of the gas , which can be converted to an output signal . Today , it is difficult to find an area on humidity , the following describes some of the problems the humidity sensor . A Select the humidity sensor measuring range selection Camshaft Sensors measuring range and measuring weight, temperature , the choice of the humidity sensor must first determine the range of measurement. In addition to weather , research departments, to engage in temperature and humidity monitoring in general do not need all wet process (0-100% RH) measurements. In today's information age , sensor technology and computer technology , automatic control closely with Zhu surgery . The purpose is to control measurement , measurement range and control of the use of collectively . Of course, do not need to engage in monitoring and control system applications are concerned, directly select universal moisture meter on it. Here are some of the application areas of the humidity sensor temperature and humidity of the different requirements for users' reference ( see Table 1 ) . Users need to raise production Crank Position Sensors measuring range , the manufacturer to ensure that users in the use of priority within the consistent performance of Engine Coolant Temperature Sensor , and seek a reasonable cost performance , in terms of both sides is a complementary thing. Second, select the humidity sensor measurement accuracy and measurement range , as the measurement accuracy of the sensor with the most important indicators. Each increase - percentage points. For sensors, is on a higher level , or even on the next level . To achieve different accuracy because its manufacturing costs vary widely , the price is also very different. For example imports an inexpensive humidity sensors only a few dollars, and one for the entire wet process of calibration and humidity sensors to a few hundred dollars , a difference of nearly a hundred times . Therefore, the user must be tailored , not the blind pursuit of "high, fine, sharp ." So first of all to control humidity temperature control is good , this is the large number of applications are often temperature and humidity - sensor integration and not simply because of the humidity sensor . In most cases, if there is no precise temperature control means , or a non- sealed space is measured , ± 5% RH of accuracy is sufficient . For applications requiring precise control of temperature and humidity of the local space , or need to keep track of changes in humidity recording of the occasion, and then use more than ± 3% RH humidity sensor accuracy . And this corresponds to the temperature sensor whose measurement accuracy ± 0.3 ℃ above shall be sufficient , at least ± 0.5 ℃ for . The accuracy better than ± 2% RH sensor calibration requirements but even the standard humidity generator is also difficult to do , not to mention Crankshaft Positioning Sensor itself . National Research Center humidity chamber article that : "Relative humidity measuring instruments , even at 20-25 ℃ under 2% RH to achieve the accuracy is still very difficult ." Third, consider the humidity sensor and temperature drift almost all sensors drift exists drift and drift . As the humidity sensor must be in contact with water vapor in the atmosphere , it is not sealed. This determines its stability and longevity is limited. Under normal circumstances , the manufacturer may indicate a second calibration of the effective use of time is 1 or 2 years , expires responsible for re-calibration. Please consider the user in selecting a good future sensor recalibration of channels , not freeloaders or superstitious foreign goods while ignoring the service asked genus.
Differential pressure sensor applications
Pressure sensors are widely used in central air conditioning, underground ventilation , boiler air supply , building automation, laboratory air pressure requirements , such as wind power wind pipe , fire engineering field of indoor air pressure control , the coal industry pressure processes. Also known as : air pressure sensor, pressure difference Automotive Temperature Sensors, wind pipe pressure sensor, indoor air air pressure sensor and so on. For measuring the automobile engine exhaust particulate filter (DPF) pressure difference before and after the exhaust channel . In order to meet emission standards , the usual method is placed in the vehicle exhaust emissions portion trap , trap tiny particles in the exhaust gas . The drawback of this method , the exhaust gas discharge passage is the accumulation of the particles trapped as being gradually blocked. Remove these particles accumulate is a location in the channel or directly in extra fuel into the exhaust gas to increase the exhaust gas temperature , in the presence of a catalyst in the trap , the exhaust gas temperature sufficient to allow the accumulated particulate combustion and gasification . This cleaning process is called "regeneration " procedure. This process there is a problem , "regeneration" process too frequently , will increase fuel consumption ; interval is too long , it will reduce engine performance. Thus, a reasonable choice of "regeneration" trigger time is very important to the pressure differential Camshaft Positioning Sensorsignal to ECU, ECU according to the pressure difference determines the accumulation of particulate trap level decision " regeneration" trigger time and the additional amount of fuel injected . Meanwhile , ECU EGR valve can be adjusted by controlling the temperature of the exhaust gas . In addition , differential pressure Engine Coolant Temp Sensor can also be used to measure gas flow , liquid level and so on. Gas flow measuring method, the flow tube and the atmospheric pressure difference between the pressure , static pressure derived flow tube , the flow rate is proportional to the square root of the static pressure , so as to arrive traffic. Determination of high and low level , low level of the pressure value measured , according to the density of the liquid , the conversion of the liquid level .
Analytical sensor signal detecting system
This concept is the detection system sensing technology developed to a certain stage of the product . Detection system sensors and measuring instruments, devices, converting the organic combination . In engineering practice , the need for multiple sensors and measuring instruments organically combined to form a whole, in order to complete the signal detection, so they formed a detection system. With computer technology and information processing technology continues to evolve , the detection system has also been involved in the content can be enriched. In the modern production process, the process parameters are automatically detected , ie detection task is done automatically by the detection system , so the research and master the structure and principles of detection systems is essential. Camshaft Position Sensor system is felt to be measured corresponding to the output size and the available output device or a device signal . Data transmission link used to transmit data . When the detection system several functional aspects independently when separated , it must be one place to another to transfer data , the data transmission link is to complete this transfer. The data processing stage is Engine Coolant Temperature Sensor output signal processing and conversion . Such as signal amplification , computing , filtering, linearization, digital to analog (D / A) or modulus (D / A) conversion, the conversion into another parameter signal or signals of a standardized uniform , so that the output signal for display , the recording can also be connected to the computer system to process information of the measured signal or to the automatic control system . data link to be measured can be sensory information into a form acceptable to people , in order to achieve monitoring , control or analysis purposes . Measurement results can be an analog display , digital display can also be used , and can be recorded by the recording apparatus or the printer will automatically print out the data . The purpose is to measure the access to be measured by measuring the true value. But in the actual measurement process, due to various reasons, for example , Crankshaft Positioning Sensor itself unsatisfactory performance , measurement method is imperfect, subject to external interference and human negligence , etc. , will result in the measured value of the measured parameters are inconsistent with the true value , the two are inconsistent The degree of measurement error representation . Error of the measured value and the true value is the difference between , which reflects the measurement accuracy. With the development of science and technology , people are increasingly demanding high accuracy , it can be said measured value of the work depends on the accuracy of measurement . When the measurement error exceeds a certain limit, measurements and measurement results would be meaningless , even give work to bring harm. Therefore, the measurement error analysis and control measurements on a technical level as well as a measure of the level of science and technology is an important aspect . However, due to the necessity of existence and universality of the error , it can only be controlled within the error range as small as possible , but not completely eliminate it. On the other hand , measurement reliability is also crucial , on different occasions , the reliability of the measurement results of different systems with different requirements . For example, when the measurement value is used as the control signal, will have to pay attention to the stability and reliability of measurement . Therefore, the measurement accuracy and reliability and other performance indicators must be measured with the specific purpose and requirements linked to adapt. Such features and characteristics of the sensor will be able to play better
Tilt sensor installation tips
Tilt sensor is an attitude sensor , mainly used in the level of detection of the object state , he has the same size of the angle measurement . Currently tilt sensor is divided into several categories, with uniaxial and biaxial inclination sensor tilt sensor , tilt sensor principle and the use made of inclinometer . Selection tilt sensor relative to other sensors , is relatively simple , relatively large number of applications on the current axis Camshaft Position Sensor , it has to have a lot of features , not just the slight angle measurement , and in different environments have different characteristics . In the choice of when we first tilt sensor to measure according to your environment, harsh environment and size requirements it is necessary to consider whether to use shell protection. The second consideration is the tilt sensor measurement accuracy and range , under normal circumstances , dual-axis tilt sensor can be selected at 360 degrees , and the measurement accuracy and output and other aspects of the problem is that the data value may be. Tilt sensor in the choice of the time is very important and that the note is that you are using the environmental problems , because of the different environment will affect most of the tilt sensor measurement results, and even some tilt sensor in certain circumstances the effect is lost . Crank Angle Sensor installed there is a certain skill , the general will have built-in tilt sensor zero adjustment , so the user can be customized according to the zero adjustment button , in order to achieve a certain function of the angle of zero . Before installing the tilt sensor , you need to determine your installation location and what you need to measure the angle relative to the plane which , for example, the angle relative to a plane , as long as Coolant Temperature Sensor is installed in a certain fixed plane , using the zero position before measuring buttons to achieve clear function , so the main point is easy to read and reduce unnecessary errors.
Deficiencies of the pressure sensor
With the development of science and technology , there is a certain pressure Crankshaft Positioning Sensor technology breakthrough in the application of increasingly widespread . But there are still many shortcomings. 1 on the basis of poor reliability of the product and manufacturing process technology research is not enough, some impact on the reliability of key technologies, such as precision machining technology, sealing technology , welding technology has not yet been well understood , which is leading products, especially the high-end product performance is not the main reason for stability and reliability . The reliability of existing national indicators of high-end products compared with foreign products , largely to a difference of 1-2 orders of magnitude. (2) product performance and functionality behind the existing domestic products in the measurement accuracy with the foreign products on an order of magnitude difference . Functionally, the current foreign products have a very high degree of intelligence . They are by the original digital information processing , better eliminate the external interference on the impact of information , thereby improving the environmental resistance of the product and measurement authenticity . The existing domestic products is still relatively low degree of intelligence . In addition, the product of the network in foreign countries has entered the practical stage , but China is basically still in its infancy . 3 Auto Temperature Sensor product technology refresh cycle is slow, the current foreign product update cycle in about 2-3 years. New technologies often can advance to reserve ten years. In China, companies often achieved through the introduction of foreign technology generation product updates , after the introduction of digestion and absorption is not well in the new product development outcomes little originality . Some adopt new principles of product in China is still in a blank state . Research institutes in the tracking of new technology , there was an achievement , but the combination of product and business oriented rather difficult. 4 Lack of developed for the use of specific solutions . Abroad in recent years, the development trend of Engine Coolant Sensor is the development or application object associated with tightly integrated software products and, ultimately, to provide users with personalized solutions.
2013年10月22日星期二
Gas sensor successfully applied petrochemical industrial gases
With the rapid development of industries and industry , some toxic gases are gradually increasing , we must take some gas detectors to detect and then make timely preventive measures . In gas detection , Camshaft Position Sensor has been great application , this paper introduces the development of Cooling Temperature Sensor and gas spill in the disposal of applications. The development of the petrochemical industry , flammable , explosive, toxic gases and range of application types have been increased . These gases in the production, transport , use the process in the event of leakage , will lead to poisoning, fire or even explosion , serious harm to people's lives and property safety. Inherent in the gas diffusion, after a leak in the external and internal concentration gradient of wind action , the gas will spread along the ground surface , is formed at the scene of explosion or combustion toxic hazards, expand hazard zone. Timely and reliable detection of the content of certain gases in the air , to take timely and effective measures to remedy , to take proper disposal methods , reducing leakage caused the accident is to avoid causing significant property and casualty necessary conditions. That's right gas detection and monitoring equipment put forward higher requirements. As an important gas detectors , Crankshaft Position Sensor has been greatly developed in recent years . Gas sensor development makes its application more widely .
Pressure of the intake pressure sensor output characteristics
Pressure of the intake pressure sensor output characteristics : EFI engine intake pressure sensor used to detect the intake air injection system called D-type ( speed density type ) . Intake pressure sensor detects intake air is not as direct as the intake flow sensor detection , instead of using indirect detection , but it also is affected by many factors, and thus the detection and repair , there are many different Cooling Temp Sensor intake air Cooling Temperature Sensor price place , the resulting failure also has its particularity. Operation of the engine , with the change in the throttle opening degree , the intake manifold vacuum , absolute pressure and the output signal characteristic curves were changed. However, changes in the relationship between them is how ? Output characteristic curve is positive or negative ? This problem is often not easy to be understood, so that some maintenance personnel at work there is a " not sure " feeling. D-type injection system is detected in the rear throttle valve inside the intake manifold absolute pressure .Throttle rear reflects both vacuum and reflects the absolute pressure , so some people think that the degree of vacuum and absolute pressure is a concept that , in fact, this understanding is one-sided. At atmospheric pressure under the same conditions ( standard atmospheric pressure of 101.3kPa), vacuum manifold higher , reflecting the manifold absolute pressure , the lower the degree of vacuum is equal to the atmospheric pressure minus the manifold absolute pressure difference of the values. The manifold absolute pressure higher , indicating that the degree of vacuum within the manifold lower manifold manifold absolute pressure equal to the outer atmospheric pressure minus the difference between the degree of vacuum . Ie the atmospheric pressure is equal to the vacuum and absolute pressure and . Understand the atmospheric pressure , vacuum, absolute pressure relationship, intake Engine Temperature Sensor output characteristic to clear.Operation of the engine , the throttle valve opening degree is smaller, the intake manifold vacuum greater manifold absolute pressure is smaller, the output signal voltage is smaller. Greater the degree of throttle opening , intake manifold vacuum is smaller, the absolute manifold pressure is greater , the output signal voltage is greater. The output signal voltage and the vacuum manifold is inversely proportional to the degree of (negative characteristics) , and manifold absolute pressure proportional to the size ( positive characteristic ) .
Analytical sensor signal detecting system
This concept is the detection system sensing technology developed to a certain stage of the product . Detection system sensors and measuring instruments, such as organic conversion device combination in engineering practice , the need for multiple sensors and measuring instruments organically combined to form a whole, in order to complete the signal detection, so they formed a detection system. With computer technology and information processing technology continues to evolve , the detection system has also been involved in the content can be enriched. In the modern production process, the process parameters are automatically detected , ie detection task is done automatically by the detection system , so the research and master the structure and principles of detection systems is essential. Camshaft Position Sensor system is felt to be measured corresponding to the output size and the available output device or a device signal . Data transmission link used to transmit data . When the detection system several functional aspects independently when separated , it must be one place to another to transfer data , the data transmission link is to complete this transfer. The data processing stage is the sensor output signal processing and conversion . Such as signal amplification , computing , filtering, linearization, digital to analog (D / A) or modulus (D / A) conversion, the conversion into another parameter signal or signals of a standardized uniform , so that the output signal for display , the recording can also be connected to the computer system to process information of the measured signal or to the automatic control system . data link to be measured can Engine Temp Sensorinformation into a form acceptable to people , in order to achieve monitoring , control or analysis purposes . Measurement results can be an analog display , digital display can also be used , and can be recorded by the recording apparatus or the printer will automatically print out the data . The purpose is to measure the access to be measured by measuring the true value. But in the actual measurement process, due to various reasons, for example , the sensor itself unsatisfactory performance , measurement method is imperfect, subject to external interference and human negligence , etc. , will result in the measured value of the measured parameters are inconsistent with the true value , the two are inconsistent The degree of measurement error representation . Error of the measured value and the true value is the difference between , which reflects the measurement accuracy. With the development of science and technology , people are increasingly demanding high accuracy , it can be said measured value of the work depends on the accuracy of measurement . When the measurement error exceeds a certain limit, measurements and measurement results would be meaningless , even give work to bring harm. Therefore, the measurement error analysis and control measurements on a technical level as well as a measure of the level of science and technology is an important aspect . However, due to the necessity of existence and universality of the error , it can only be controlled within the error range as small as possible , but not completely eliminate it. On the other hand , measurement reliability is also crucial , on different occasions , the reliability of the measurement results of different systems with different requirements . For example, when the measurement value is used as the control signal, will have to pay attention to the stability and reliability of measurement . Therefore, the measurement accuracy and reliability and other performance indicators must be measured with the specific purpose and requirements linked to adapt. So that Crankshaft Positioning Sensor functions and features can better play out !
Select the humidity sensor measurement accuracy
And the same measurement range , measurement accuracy of the sensor with the most important indicators. Each increase - percentage points. It is for the sensor to a higher level , or even on the next level . To achieve different accuracy because its manufacturing costs vary widely , the price is also very different. For example imports an inexpensive humidity sensors only a few dollars, and one for the entire wet process of calibration and Camshaft Positioning Sensor to a few hundred dollars , a difference of nearly a hundred times . Therefore, the user must be tailored , not the blind pursuit of "high, fine, sharp ."Manufacturers often give its humidity sensor segmentation accuracy . Such as the low temperature section ( 0 a 80% RH) was ± 2% RH, and the humidity sections (80-100% RH) was ± 4% RH. And this accuracy is at a specified temperature (such as 25 ℃) value. If used at different temperatures and humidity sensors. Its indication should also consider the impact of temperature drift . Is known , the relative humidity is a function of temperature , temperature seriously affecting the relative humidity within the specified space . Each change of temperature 0.1 ℃. Will generate 0.5% RH humidity change (error ) . If it is difficult to do using the occasion thermostat , the proposed high measuring precision is inappropriate. Because humidity variations with temperature drift suddenly uncertain , then talk about measuring precision will be moot .So first of all to control humidity temperature control is good , this is the large number of applications are often temperature and Car Temperature Sensor integration and not simply because of the humidity sensor .
In most cases, if there is no precise temperature control means , or a non- sealed space is measured , ± 5% RH of accuracy is sufficient . For applications requiring precise control of temperature and humidity of the local space , or need to keep track of changes in humidity recording of the occasion, and then use more than ± 3% RH humidity sensor accuracy . And this corresponds to the temperature sensor. Its measurement accuracy ± 0.3 ℃ above shall be sufficient , at least ± 0.5 ℃ for . The accuracy better than ± 2% RH sensor calibration requirements but even the standard humidity generator is also difficult to do , not to mention the sensor itself . National Research Center humidity chamber article that : "Relative humidity measuring instruments , even at 20-25 ℃ under 2% RH to achieve the accuracy is still very difficult ."
Third, when considering the Crank Shaft Position Sensor drift and drift
Almost all of the sensors are present when the drift and drift . As the humidity sensor must be in contact with water vapor in the atmosphere , it is not sealed. This determines its stability and longevity is limited. Under normal circumstances , the manufacturer may indicate a second calibration of the effective use of time is 1 or 2 years , expires responsible for re-calibration. Please consider the user in selecting a good future sensor recalibration of channels , not freeloaders or superstitious foreign goods while ignoring the service asked genus.
Tilt sensor installation tips
Tilt sensor is an attitude sensor , mainly used in the level of detection of the object state , he has the same size of the angle measurement . Currently tilt sensor is divided into several categories, with uniaxial and biaxial inclination sensor tilt sensor , tilt sensor principle and the use made of inclinometer . Selection tilt sensor relative to other sensors , is relatively simple , relatively large number of applications on the current axis Camshaft Position Sensor, it has to have a lot of features , not just the slight angle measurement , and in different environments have different characteristics . In the choice of when we first tilt sensor to measure according to your environment, harsh environment and size requirements it is necessary to consider whether to use shell protection. The second consideration is the Coolant Temp Sensormeasurement accuracy and range , under normal circumstances , dual-axis tilt sensor can be selected at 360 degrees , and the measurement accuracy and output and other aspects of the problem is that the data value may be. Tilt sensor in the choice of the time is very important and that the note is that you are using the environmental problems , because of the different environment will affect most of the tilt sensor measurement results, and even some Crankshaft Sensor Replacement in certain circumstances the effect is lost . Tilt sensor installed there is a certain skill , the general will have built-in tilt sensor zero adjustment , so the user can be customized according to the zero adjustment button , in order to achieve a certain function of the angle of zero . Before installing the tilt sensor , you need to determine your installation location and what you need to measure the angle relative to the plane which , for example, the angle relative to a plane , as long as the sensor is installed in a certain fixed plane , using the zero position before measuring buttons to achieve clear function , so the main point is easy to read and reduce unnecessary errors.
People sleep quality analysis of the pressure sensor
Pressure Sensor interesting applications are emerging , recently the University of Helsinki Department of Computer Science, Software Development Team utilize the sensor data analysis developed a computer software , it is interesting is that this software can automatically obtain sleeper sleep data and converts into musical form , see the quality of sleep people to find the right music to promote sleep , the current application has been composing music can access through its official website , this technology in software engineering caused a lot of repercussions. Then this is how to achieve it, a brief today , which uses a Crankshaft Positioning Sensor to the basic principle of the pressure sensor on the mattress underground , of course, Coolant Temperature Sensor is a high sensitivity. The sensor analyzes the information is sleeping person's turn , heartbeat and breathing -related sleep action to infer what people in a state of sleep , and then through the analysis of Engine Water Temperature Sensor , the sensor signal obtained collecting heartbeat and breathing rhythm of sleep data , Finally, all data processing spectrum into a section of track, of course, a night 's sleep you can be compressed into a few minutes of music. Professor at the University of Helsinki relevant reports to explain their research mentioned that they are working on developing a new way to interpret or directly from the fact that abstract data experience to experience . Music can evoke similar emotions to express a lot of people nature of the data , which is a natural sleep analysis -based applications. The source of inspiration for the development of the software before the college graduates in the development of a sleep state analysis service software, this software combines the sensor data analysis, creating this interesting and practical applications, but also will bring a lot of patients with insomnia Help .
Deficiencies of the pressure sensor
With the development of science and technology , there is a certain pressure
Crankshaft Positioning Sensor technology breakthrough in the application of increasingly widespread . But there are still many shortcomings. 1 on the basis of poor reliability of the product and manufacturing process technology research is not enough, some impact on the reliability of key technologies, such as precision machining technology, sealing technology , welding technology has not yet been well understood , which is leading products, especially the high-end product performance is not the main reason for stability and reliability . The reliability of existing national indicators of high-end products compared with foreign products , largely to a difference of 1-2 orders of magnitude. (2) product performance and functionality behind the existing domestic products in the measurement accuracy with the foreign products on an order of magnitude difference . Functionally, the current foreign products have a very high degree of intelligence . They are by the original digital information processing , better eliminate the external interference on the impact of information , thereby improving the environmental resistance of the product and measurement authenticity . The existing domestic products is still relatively low degree of intelligence . In addition, the product of the network in foreign countries has entered the practical stage , but China is basically still in its infancy . 3Shaft Position Sensor product technology refresh cycle is slow, the current foreign product update cycle in about 2-3 years. New technologies often can advance to reserve ten years. In China, companies often achieved through the introduction of foreign technology generation product updates , after the introduction of digestion and absorption is not well in the new product development outcomes little originality . Some adopt new principles of product in China is still in a blank state . Research institutes in the tracking of new technology , there was an achievement , but the combination of product and business oriented rather difficult. 4 Lack of developed for the use of specific solutions . Abroad in recent years, the development trend of Auto Temperature Sensor is the development or application object associated with tightly integrated software products and, ultimately, to provide users with personalized solutions.
What factors affect the resonant frequency of the sensor
Cutoff frequency is the frequency at the required frequency response of the sensor can be measured within the amplitude error signal of the highest frequency . High cut-off frequency directly related to the size and the error value , a predetermined error range then the corresponding frequency is relatively high cut-off frequency . Frequency characteristics of piezoelectric sensor depends on the sensor mechanical resonance frequency of the first order , the actual use of the first-order resonant frequency of the sensor is often mounted resonant frequency. Resonance frequency by the internal sensor sensitive to the natural frequency of the core and the overall quality of Shaft Position Sensor and mounting the coupling rigidity integrated decision. Resonance frequency of the sensor will directly affect the level of the high frequency range , so in a stable resonance frequency sensitive core under the premise of improving the mounting coupling stiffness important condition to ensure high-frequency measurements . The sensor is installed in the form sensor manufacturers to provide high frequency cutoff frequencies are in a more ideal installation conditions obtained . The actual use of different forms of sensor installation and installation quality is good or bad will directly affect the installation coupling stiffness, thereby changing Positioning Sensor measurement frequency cutoff frequency. Different installation methods that correspond to different characteristics of the resonant frequency has been installed in many vibration measurement is described in the literature ; it is necessary that the different forms of the installation when combined together, the sensor response will be the lowest frequency of the frequency response of the installation form constraints . High frequency measurements of the installation screws are often used form . In order to achieve the desired results , the test object is necessary to achieve the required surface flatness and finish requirements and the sensor should be installed at the specified torque in order to raise as much as possible to ensure the sensor mounting rigidity coupled high-frequency cutoff frequency. Sensor cutoff frequency the higher the frequency of Coolant Temperature Sensor installation requirements are higher , so the user using a high frequency measurement sensors sensor installation must be taken seriously . Sensor output connectors and cables form the impact of the measurement signal sensor signal output connectors are also potential important factors affecting high-frequency measurements . In practical applications the sensor connector and cable are also part of the sensor . Various forms of connectors, cable connector and the sensor is connected , and the weight of the cable and the cable fixed with respect to the form of the measured object will directly affect the sensor 's resonant frequency. The lighter weight of the sensor , connectors and cables for high frequency measurements of the more significant. So when the installation conditions permit small high-frequency measuring sensor connector form should be considered first conjoined cable , conjoined cable has fewer moving parts , light weight , more suitable for high frequency measurements.
How to choose the displacement sensor
Moving objects in real life is very common , and usually we do not to pay attention to the amount of movement of objects , but in the relevant industry, water level measurement or control other aspects need to know that the amount of change is. Scientific measurement of displacement change is necessary to use a displacement sensor . The so-called displacement sensor is a system device , as a measurement device displacement sensor in many applications played a key role. It is used to measure the mechanical displacement of the instrument, and industrial processes change the displacement machine . Displacement sensor in accordance with the signal output can be divided into analog and digital displacement sensor displacement sensor . Usually we see resistive capacitive and inductive eddy current and other such are analog displacement sensor , which is characterized by a unified simple in structure . Relative to the digital displacement measuring sensor is a displacement output into a digital read directly , as opposed to analog displacement sensor is relatively complex , it has the advantage of a relatively high accuracy of measurement , more accurate and more enough read the measured displacement variation. Displacement Crankshaft Positioning Sensor has a high accuracy requirements, such as the ambient temperature constant respect the requirements for precise control of the movement mechanism requirements . At present, the displacement of the sensor for the detection of the installation , developers have developed a laser displacement sensor , which uses the principle of echo to measure distance to achieve a certain degree of accuracy. Inside the Camshaft Positioning Sensorby the processor unit , the echo processing unit , the laser transmitter , laser receiver and other components. Currently in production industry displacement sensors and displacement detection distance is the most popular topic. Maybe not the ultimate goal to measure displacement , and displacement changes the size and level of accuracy required for a range of issues are to correspond to what kind of applications up . Coolant Temp Sensorbuyers need to understand the working principle of displacement sensors and displacement sensor installation methods to know how to Selection . Displacement sensors and other sensors like the reality is that the amount of change finally converted to an electric signal. Generally based on changes in the size of the displacement and the user needs to decide the choice of what precision sensors, consider the good of its error , it is considered a good travel distance corresponding to the user's application environment is an impact on the data collection and so on . Similarly displacement sensor is sensitive devices, the time of purchase is necessary to use caution precautions so that the sensor has a longer service life .
订阅:
博文 (Atom)